Introduction
In aircraft maintenance, mechanical and electrical hazards pose significant risks to both workers and equipment. Identifying, assessing, and mitigating these hazards is essential for maintaining a safe work environment and ensuring aircraft safety. This post covers the specific mechanical and electrical risks common in aircraft maintenance and provides strategies for effective hazard management, including the latest industry practices and compliance updates.
1. Understanding Mechanical Hazards in Aircraft Maintenance
- What Are Mechanical Hazards?
Mechanical hazards arise from interactions with machinery, tools, or moving components. Common mechanical risks in aircraft maintenance include cuts, crush injuries, falls, and contact with rotating parts. - Key Risks:
- Pinch Points and Crush Injuries: Handling large components or working near machinery with rotating parts can lead to pinch points and crush injuries.
- Sharp Edges and Tools: Maintenance often involves working with sharp tools and edges, increasing the risk of cuts and punctures.
- Falls from Heights: Maintenance tasks may require accessing elevated areas, posing a risk of falls if proper safety protocols aren’t followed.
2. Strategies for Mitigating Mechanical Hazards
- Using Proper Personal Protective Equipment (PPE)
Ensure all personnel use the correct PPE for mechanical tasks, such as cut-resistant gloves, steel-toe boots, and safety goggles. PPE acts as a first line of defense. - Lockout/Tagout (LOTO) Procedures
The LOTO procedure ensures that machinery is properly shut off and cannot be turned back on while maintenance is performed. Regularly reinforce LOTO training to prevent accidental activation of equipment. - Engineering Controls
Use physical barriers or machine guards to protect workers from moving parts. These controls prevent direct contact with hazardous components, reducing the likelihood of injury. - Training and Safe Work Practices
Conduct regular training sessions on the risks of mechanical hazards and safe handling practices for tools and equipment. Reinforcing safe work practices minimizes human error and increases awareness.
3. Identifying Electrical Hazards in Aircraft Maintenance
- Common Electrical Risks:
Electrical hazards are especially dangerous because they can result in shocks, burns, or even fatalities. In aircraft maintenance, working with electrical systems or exposed wiring presents specific risks.- Electric Shock: Direct contact with live wires or improperly grounded equipment can lead to electric shocks.
- Arc Flash: An arc flash can occur when there’s a fault in the electrical circuit, releasing energy in the form of heat and light.
- Static Electricity: Working with fuel systems and electrical components can lead to static buildup, which may cause a fire if discharged improperly.
- Recent Updates for 2024:
New safety standards emphasize the use of advanced insulation techniques and materials that minimize the risk of electric shock. Compliance guidelines now also include regular checks for wiring integrity.
4. Controlling Electrical Hazards in Aircraft Maintenance
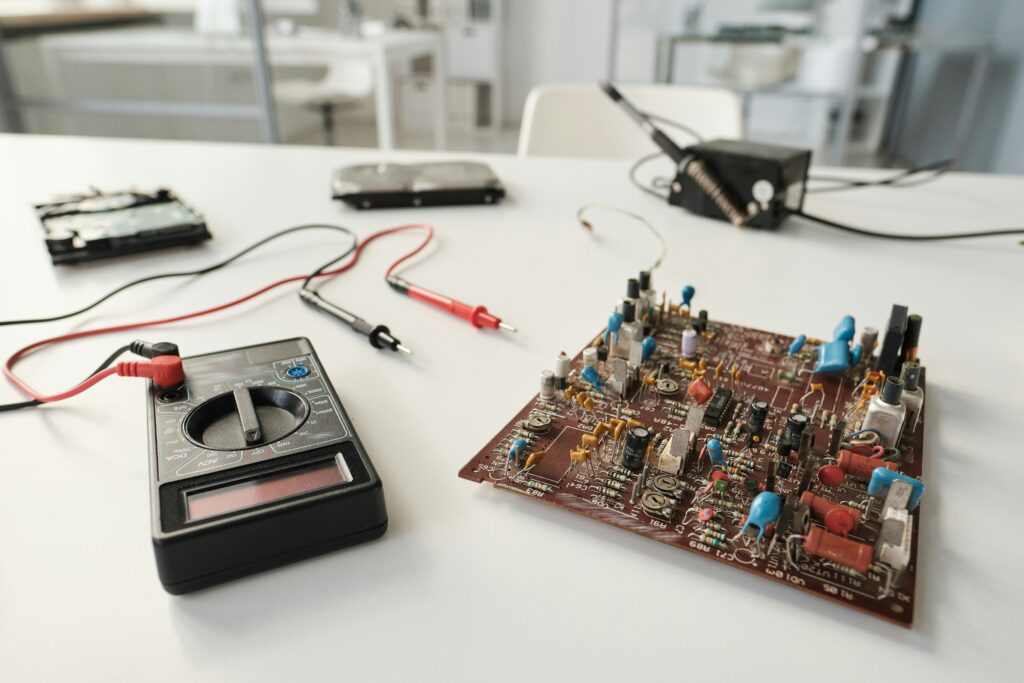
- Implementing Grounding and Bonding Techniques
Grounding electrical equipment and bonding conductive parts prevents static discharge, significantly reducing the risk of electric shocks and fires. - Regular Inspections and Maintenance
Conduct routine inspections of electrical systems, wiring, and tools to detect wear, corrosion, or other issues. Addressing these problems early prevents escalation and ensures compliance. - Using Insulated Tools and Protective Equipment
Equip maintenance personnel with insulated tools and PPE designed for electrical work, such as rubber gloves and safety glasses. Insulated tools add an extra layer of protection during high-risk tasks. - Arc Flash Safety Protocols
Instruct workers to follow arc flash safety protocols, including wearing flame-resistant clothing and maintaining a safe distance from live circuits.
5. Regulatory Compliance for Mechanical and Electrical Safety
- OSHA and FAA Guidelines
In 2024, OSHA and the FAA updated guidelines for mechanical and electrical safety in aircraft maintenance environments. New regulations focus on continuous training and proactive inspections. - Risk Assessment Integration
Incorporate mechanical and electrical hazard management into your overall risk assessment process. The FAA’s Risk Management Handbook (FAA-H-8083-2A) provides a comprehensive approach to identifying and mitigating these specific hazards.
6. Steps to Conduct Hazard-Specific Risk Assessments
- Step 1: Identify Potential Mechanical and Electrical Hazards – Walk through the maintenance area, identifying machinery and electrical components with high-risk factors.
- Step 2: Evaluate Risks – For each hazard, assess the likelihood and severity, prioritizing high-risk items.
- Step 3: Apply Control Measures – Based on your assessment, apply relevant control measures, such as PPE for mechanical tasks or insulated tools for electrical work.
- Step 4: Document and Review – Keep detailed records of each risk assessment and conduct reviews regularly to identify new hazards or changes in equipment.
- Step 5: Team Training and Engagement – Ensure all team members receive training on mechanical and electrical hazard management. Reinforce training through safety briefings and visual aids.
Additional resource
- FAA Risk Management Handbook (FAA-H-8083-2A)
- OSHA Safety and Health Topics: Aircraft Maintenance
- Part one of this article series!
Conclusion
Effectively managing mechanical and electrical hazards in aircraft maintenance requires a combination of proactive risk assessment, proper training, and adherence to regulatory standards. By implementing the right control measures and regularly reviewing hazard protocols, maintenance teams can significantly reduce risks and improve safety outcomes. The next article in our series will explore chemical and environmental hazard management in aircraft maintenance, delving into practices that minimize exposure to harmful substances and environmental risks.