Introduction
In the demanding field of aircraft maintenance, managing chemical and environmental hazards is critical. Exposure to hazardous chemicals, extreme temperatures, and loud noise can pose serious health risks for technicians and affect the safety of aircraft operations. This guide explores common chemical and environmental hazards in aircraft maintenance, outlining best practices for identifying, assessing, and controlling these risks.
1. Understanding Chemical Hazards in Aircraft Maintenance
- What Are Chemical Hazards?
Chemical hazards arise from exposure to substances used in maintenance, including degreasers, solvents, hydraulic fluids, and paints. Prolonged exposure or improper handling of these chemicals can lead to respiratory problems, skin irritation, and long-term health issues. - Key Chemical Risks:
- Inhalation of Toxic Fumes: Many chemicals emit harmful fumes that can cause respiratory issues if inhaled regularly.
- Skin and Eye Irritation: Direct contact with chemicals can lead to burns, rashes, and eye irritation.
- Long-Term Health Effects: Chronic exposure to certain chemicals may increase the risk of diseases like cancer, especially if proper protection measures aren’t in place.
Additional Resource: For more information on hazardous chemicals in the workplace, refer to OSHA’s Hazardous Materials Guidelines.
2. Strategies for Mitigating Chemical Hazards
- Using Personal Protective Equipment (PPE)
PPE is the first line of defense against chemical hazards. Technicians should use gloves, safety goggles, and respirators as necessary to protect against harmful exposure. Ensure that all PPE is properly rated for the chemicals in use. - Ventilation and Local Exhaust Systems
Proper ventilation reduces airborne contaminants in the workspace, minimizing the risk of inhaling toxic fumes. Installing local exhaust systems can help capture fumes directly at the source. - Safe Storage and Labeling
Storing chemicals safely and labeling them accurately is essential to prevent accidental exposure or misuse. Use OSHA-compliant labels and ensure that chemicals are stored in designated areas away from incompatible substances. - Regular Safety Training
Training personnel on chemical hazards, proper handling, and first-aid measures is key to preventing incidents. Regularly reviewing safety protocols ensures everyone is prepared for safe handling.
3. Identifying Environmental Hazards in Aircraft Maintenance
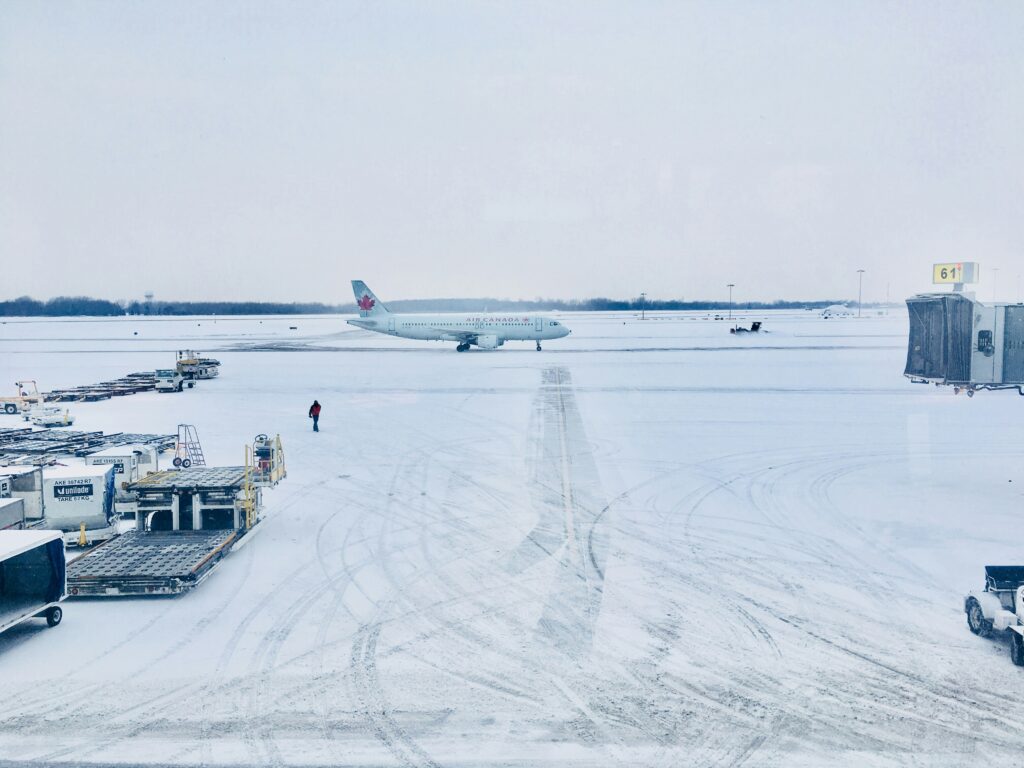
- Common Environmental Risks:
Environmental hazards include factors like temperature extremes, noise, and inadequate lighting, all of which can affect worker health and safety.- Extreme Temperatures: Maintenance often takes place in non-climate-controlled hangars, exposing workers to high heat or freezing conditions.
- Noise Pollution: Aircraft engines and machinery generate high noise levels that can lead to hearing loss over time.
- Poor Lighting: Insufficient lighting increases the risk of accidents and reduces the accuracy of maintenance tasks, particularly during inspections.
- 2024 Update: New safety standards now emphasize the importance of environmental controls, including enhanced ventilation and noise protection requirements for maintenance areas.
Additional Resource: For a comprehensive guide on managing environmental hazards, check OSHA’s Environmental Controls and Safety Guidelines.
4. Controlling Environmental Hazards
- Temperature Control
Use portable heating or cooling units to manage extreme temperatures in maintenance areas. Scheduling tasks during less extreme times of day and providing breaks in temperature-controlled environments can also help prevent heat or cold stress. - Noise Reduction
Equip workers with hearing protection, such as earmuffs or earplugs, rated for high-decibel environments. Additionally, consider placing sound barriers around high-noise areas to minimize overall exposure. - Improving Lighting
Install high-quality, adjustable lighting in maintenance areas to ensure that technicians can see clearly, reducing the risk of errors and accidents. LED lights are often effective for creating a well-lit workspace.
5. Regulatory Compliance for Chemical and Environmental Safety
- OSHA Guidelines
OSHA provides detailed regulations for managing chemical and environmental hazards, including standards for safe chemical handling, PPE requirements, and permissible noise exposure limits. Regular compliance audits ensure adherence to these standards. Learn more about OSHA’s standards for workplace safety. - FAA Guidance
The FAA emphasizes risk management procedures to address hazards like chemical exposure and environmental risks. For more on these safety protocols, refer to the FAA’s Risk Management Handbook (FAA-H-8083-2A). - Material Safety Data Sheets (MSDS)
MSDS documents provide critical information on each chemical’s properties, hazards, and first-aid measures. Maintaining accessible MSDS files allows technicians to quickly reference safety information in case of exposure.
Conclusion
Managing chemical and environmental hazards in aircraft maintenance requires proactive risk assessment and strict adherence to safety protocols. With proper PPE, environmental controls, and compliance with regulatory guidelines, maintenance teams can significantly reduce the risks associated with hazardous chemicals and extreme conditions. In the next part of this series, we will explore ergonomic hazards and the importance of proper workplace design in aircraft maintenance safety.
Check out other articles from our series at https://safetygearinsights.com/blog/